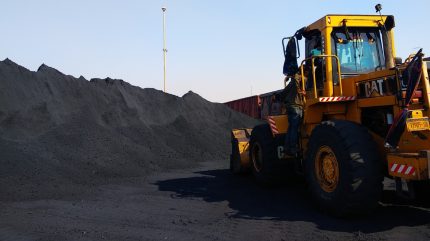
Several mines around the world are leading the way in adopting electric vehicles (EVs) to enhance sustainability and reduce carbon emissions.
For example, industry giants such as BHP and Rio Tinto are collaborating with Komatsu and Caterpillar on trial operations to accelerate the deployment of battery-electric haul trucks across their operations.
Nouveau Monde’s Matawinie graphite mine in Quebec, Canada, plans to use 12 electric trucks to save more than 80,000l of diesel per year, with a corresponding reduction in greenhouse gas (GHG) emissions. Similarly, BHP is collaborating with Caterpillar and Komatsu to trial battery-electric haul trucks in its Pilbara iron ore operations in Australia to reduce carbon emissions and achieve net zero by 2050.
These initiatives reflect a growing commitment within the mining industry to embrace cleaner technologies and reduce their environmental footprint.
In Asia and notably in China, the electric mining dump truck industry is rapidly evolving, driven by an objective to reduce emissions and enhance sustainability in mining operations. Leading Chinese manufacturers such as Tonly, Lingong Heavy Machinery (LGMG), and XCMG are playing a key role in this transformation.
In Indonesia, Vale is testing 100% electric 72t trucks at its Sorowako mine. These innovations are pivotal in promoting greener mining practices and reducing the environmental impacts of the industry.
In Pakistan, SECMC is the first mining company in the country to incorporate EVs into its practices. The entity has been operating a fleet of over 200 diesel units with a payload capacity ranging between 60t and 90t. This has significantly impacted costs, with fuel typically contributing 30%-50% of operational expenditures. SECMC has introduced four EV trucks on trial operations to assess the performance of these vehicles in terms of load profile, power consumption, reverse charging and vehicular impact amid harsh weather conditions (above 50°C).
The commercialisation of electric mining trucks is also underway by original equipment manufacturers (OEMs). All the major OEMs are investing heavily in creating prototypes and testing their performance under the demanding environments of mining operations such as adverse temperatures, heavy loads, and rough terrains. Additionally, commercial-scale mines are also implementing rigorous safety protocols and environmental management systems to ensure sustainable and responsible mining practices.
The transition to electric mining dump trucks presents several advantages and challenges.
Technical considerations for operating electric trucks
Haul road gradient: One of the major constraints for EVs in mining is the selection of appropriate routes, as the battery performance can vary. Under loaded conditions on downhill slopes ranging from 6% to 8%, the truck requires charging every few days. Operating heavy-loaded EV mining dump trucks on downhill gradients saves significant energy, over 90%. However, for deeper mines with uphill loaded conditions with gradients exceeding 5%, multiple battery exchanges are needed throughout the day to maintain optimal performance, creating downtime and production delays. Some companies are integrating the trolley systems with EVs to cope with this challenge while others are working with battery swapping.
Range limitations: Battery technology currently may not support the long-distance, heavy-duty demands of mining. Charging time and battery life can impact operational efficiency. However, ongoing advancements in battery technology, such as setting up megawatt charging stations (MCS), can reduce the charging time. Typically, a 400 kilowatt-hour (kWh) battery is charged in 90 minutes, but with the introduction of new technology, the charging time is reduced to 12kWh/min.
High torque: Unlike traditional internal combustion engines, EVs provide maximum torque almost instantaneously, resulting in powerful and smooth acceleration. This instant torque availability will enhance the performance and efficiency of mining operations, particularly in demanding conditions.
Charging Infrastructure: Charging infrastructure is a challenge, particularly in remote mining sites. However, solutions such as renewable energy sources, mobile charging units, and battery swapping stations are being explored to overcome these barriers.
Grid stability: The increased demand for electricity to charge a fleet of EV trucks can strain the local power grid, potentially leading to instability and outages. Integrating renewable energy sources, such as solar or wind power, with energy storage systems can help stabilise the grid. On-site renewable energy generation can reduce reliance on the grid and provide a sustainable power source for charging EVs.
Ambient weather: Weather conditions affect battery performance, with cold temperatures reducing capacity and high heat causing overheating. Advances in battery thermal management and weatherproofing will help address these issues.
Economic analysis of EVs in mining
Cost savings and efficiency: Electric trucks can significantly reduce operational costs compared to diesel-powered trucks. The regenerative braking system in EVs recovers energy during downhill operations, leading to substantial savings. This energy recovery can lower operational costs by reducing the frequency and cost of recharging. EVs also have fewer moving parts than diesel trucks, resulting in lower maintenance costs. This includes savings on engine oil, filters, and other consumables.
Capital and operating expenditure: EVs can require double the capital expenditure of diesel trucks, when considering the cost of purchasing the trucks, installing charging infrastructure and setting up battery swapping/charging stations. On the other hand, EV trucks have fewer moving parts and require less maintenance/repair, contributing to a 20-30% reduction in operational expenditure over the life of the vehicle with a payback period of 4-5 years. By integrating EV trucks into our fleet, we can improve the availability of our trucks, ensuring smoother and more efficient mining operations.
Power consumption: As highlighted above, the power consumption of an EV depends upon various factors such as haul road gradients, temperature and site conditions. However, the power tariff plays a crucial role in the economics of EVs. With a reduction in renewable tariffs and recent developments in battery-energy storage system (BESS) technologies, EVs can be a competitive alternative to diesel trucks. Furthermore, there could be savings up to 30%-40% in terms of fuel consumption if site conditions are suitable for EVs.
Environmental considerations
A typical diesel truck consumes 0.8l – 1.2l of fuel per bank cubic metre (BCM) of waste, and each litre of diesel emits 2.6kg of CO₂. Based on this, the total CO₂ emissions for transporting 100,000 BCM of waste would be 312 tonnes per day. By integrating zero-emission EV trucks into our fleet, we can significantly reduce these emissions. This shift will also contribute to cleaner and more sustainable mining operations.
Looking to the future
Many mining operations are dealing with ageing equipment that needs to be retired. Transitioning to EV trucks provides an excellent opportunity to replace outdated machinery with modern, efficient, and environmentally friendly alternatives. This will not only enhance operational efficiency but also ensure compliance with evolving environmental regulations. Furthermore, the shift to electric dump trucks offers an economic opportunity.
By reducing operational expenditures and enhancing the availability and efficiency of mining operations, EV trucks offer a viable path forward for the industry.
As the global market shifts towards sustainability, early adoption of EVs will ensure long-term viability and competitiveness. Companies that delay this transition may face higher costs and regulatory pressures in the future.
About the author: Arsalan Anwar is Manager – Technical & Mine Expansion at Sindh Engro Coal Mining Company. He is responsible for developing and implementing short, intermediate and long-term strategies that supports operational growth.